PET Preform Injection Molding: Process, Benefits, and Key Differences
The plastic injection molding process in which molten plastic is injected into a mold cavity, cooled, and solidified to form a final product is highly efficient and cost-effective, making it the preferred method for mass production of plastic components across various industries. Injection molding allows for high precision, repeatability, and scalability, making it a key technology in modern manufacturing across a wide scale of applications and industries.
Understanding PET Preform Injection Molding
PET (Polyethylene Terephthalate) preform injection molding is a specialized manufacturing process devoted to producing polymer preforms that can be subsequently blown into finished containers, such as bottles. As part of the plastic injection molding industry, PET preform molding leverages the unique properties of PET resin, including its strength, barrier performance, and processing versatility, making it an ideal choice for various applications, primarily in the packaging sector.
The injection molding process itself is highly efficient, contributing to the rapid production of high-quality preforms with consistent accuracy. This method involves melting PET granules and injecting them into a mold where they cool and solidify, forming preforms that can later be reshaped into final products through subsequent processes like blow molding. The relevance of PET preform injection molding techniques extends across various industries, including food, beverage, pharmaceuticals, and more, owing to its capability to produce lightweight yet durable products that meet stringent regulatory standards.
As sustainability concerns rise, PET’s recyclability further enhances its appeal, supporting the shift toward eco-friendly manufacturing practices. This article explores the step-by-step process behind PET preform injection molding, its benefits, the differences compared to other molding methods, and the vital role it plays in fostering a circular economy.
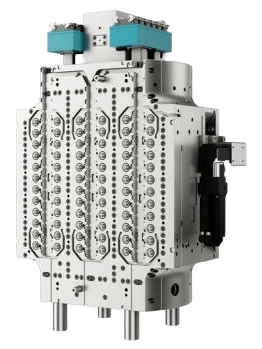
Contact +1 (908) 281-0055 or sales@polymercleaning.com to discuss your Hot Runner Systems today! Experts in Hot Runner System Repair and Maintenance for all OEM.
1. PET Preform Injection Molding Process
The PET preform injection molding process can be segmented into several critical stages. Each step is meticulously designed to ensure that the final products meet both quality and performance specifications.
Step 1: Material Preparation
The process begins with the selection of high-grade PET resin. The resin pellets are dried to a specific moisture level; this is crucial since moisture can lead to defects during the melting process. Typically, pre-drying occurs in a desiccant dryer, which effectively removes moisture.
Step 2: Injection Molding
Once dried, the PET pellets are fed into the injection molding machine’s hopper. The machine’s screw then conveys the pellets through a heated barrel, where they are melted at temperatures typically between 240°C and 270°C. The molten PET is injected into a preform mold under high pressure; this ensures that the material fully fills the cavity for a uniform preform shape.
Step 3: Cooling
After injection, cool water circulates through the mold to facilitate rapid cooling of the preform. This step solidifies the preform, allowing it to retain its shape. Cooling durations may vary based on the thickness of the preform and the specific design of the mold.
Step 4: Ejection
Once adequately cooled, the preforms are ejected from the mold using mechanical ejection pins. Proper ejection is vital to avoid damages; thus, mold design often incorporates features to support smooth ejection, minimizing risks of any defects.
Step 5: Inspection and Quality Control
Post-ejection, preforms undergo rigorous inspection for quality control. Engineers check for dimensional accuracy, surface finish, and any other flaws. High standards of quality ensure that subsequent blow molding processes yield flawless finished products.
This breakdown of PET preform injection molding highlights the intricacies involved in producing high-quality preforms, empowering industry professionals to understand not just the process but also its robust potential for varied applications.
2. Key Benefits of Using PET in Injection Molding
The selection of PET injection molding brings several inherent advantages that make it a preferred option across different industries.
High Strength & Durability
PET exhibits remarkable strength and durability, capable of withstanding substantial impact and stress without deformation. This characteristic makes it suitable for applications requiring robust packaging solutions. Research indicates that PET’s tensile strength is significantly higher than that of many other plastics, providing assurance for storing products under varying environmental conditions (Kumar et al., 2020).
Recyclability & Sustainability
One of the primary drivers for PET’s popularity is its recyclability. PET is one of the most recycled plastics globally, with a recycling rate of approximately 29% in many regions. The ability to reincorporate recycled PET into new products not only reduces the environmental footprint but also aligns with global sustainability initiatives (Geyer et al., 2017).
Clarity & Aesthetic Appeal
For packaging applications, clarity is essential. PET provides superior clarity, making it ideal for beverage bottles and cosmetic containers where product visibility enhances consumer appeal. Its aesthetic qualities contribute to branding and marketing strategies that rely on visual impact.
Lightweight yet Rigid
Compared to other materials, PET is lightweight, making it easier to transport and handle. Despite being lightweight, it does not compromise on rigidity, allowing it to replace heavier alternatives in various structural applications without sacrificing performance.
These benefits underscore the advantages of adopting PET as a material of choice in injection molding processes while fostering sustainability and promoting transparency in product packaging.
3. How PET Preform Injection Molding Differs from Other Plastic Injection Molding Methods
Understanding the distinctions between PET preform injection molding and other plastic injection methodologies is crucial for industry experts. While the fundamental principles of injection molding remain constant—melt-convey-inject-cool-eject—specific variances arise from the materials and end-application.
Material Composition
Different plastic materials possess unique chemical properties influencing their processing and performance. For instance, while PET is well-suited for applications due to its thermal stability and mechanical strength, materials like Polypropylene (PP) or Polyethylene (PE) offer different benefits such as cost-effectiveness and flexibility. Consequently, the suitable method for each material can vary based on application requirements.
Temperature and Processing
Manufacturing with PET requires specific temperature control and processing settings; PET needs precise heating to avoid hydrolysis, a common issue with other polymers. The molding temperature significantly affects crystallinity and structural integrity, which differs from methods used for other plastics. Specifically, PET usually operates at higher temperatures than traditional materials like PP.
End-Use Applications
The scope of applications for PET preform injection molding often includes high-value consumer products like beverage packaging, where protection against oxygen permeation and moisture retention is critical. In contrast, other methods may cater primarily to applications requiring lower tensile strength or impact resistance.
Ultimately, recognizing these differences enhances the technical competence of industry professionals, informing their choices in material selection, application design, and production techniques.
4. Industry Applications of PET Preform Injection Molding
PET preform injection molding serves a wide array of industries, primarily owing to its adaptability and the diverse properties of PET. Some of the most notable applications include:
Food and Beverage Packaging
The food and beverage industry is perhaps the most significant consumer of PET preforms. From water bottles to carbonated beverage containers, PET’s barrier properties ensure product integrity while delivering aesthetic appeal. The lightweight nature of PET also facilitates shipping and reduces logistical costs.
Pharmaceutical Containers
Packaging in the pharmaceutical sector requires strict compliance with safety and quality standards. PET preforms are often utilized to manufacture oral medication containers, ensuring content protection and stability while allowing for precise dosages.
Cosmetic Packaging
The cosmetic industry has gravitated towards PET preform injection molding for packaging lotions, creams, and other beauty products. The clarity and aesthetic qualities of PET not only allow consumers to view product contents but also enhance brand perception.
Industrial Applications
Beyond consumer products, PET preforms are also used in various industrial applications, including chemical containers and agricultural containers, where strength and durability are paramount.
The versatility of PET preform injection molding ensures its sustained relevance across several industries, fostering innovation and efficiency along the entire manufacturing chain.
5. Sustainability: The Role of PET in a Circular Economy
Sustainability initiatives are reshaping the landscape of plastic manufacturing, with PET playing a pivotal role in the development of a circular economy. The recycling potential of PET has garnered significant attention as industries strive to minimize their environmental impact.
Recycling PET in Injection Molding
Recycling PET for injection molding presents distinct challenges and advantages. The recycling process involves collecting used PET containers, cleaning them, and conducting a mechanical recycling process. While contamination and degradation of material quality present challenges, advancements in recycling technologies have yielded solutions, including chemical recycling, which allows for the restoration of the original polymer properties.
How PET Contributes to Sustainability Goals
By incorporating recycled PET into new products, manufacturers can significantly decrease their carbon footprint and energy consumption. Furthermore, using recycled materials can reduce dependence on virgin resources, aligning production practices with sustainability frameworks and regulatory requirements.
Future Trends in Eco-Friendly Plastic Molding
The future of eco-friendly plastic molding is promising, with ongoing innovations in material sciences and recycling technologies. Emerging trends include the increased use of bio-based PET (biodegradable PET variants) and the development of advanced molds that facilitate the processing of recycled materials. Continuous improvement in recycling rates and circularity practices is expected to drive the adoption of PET in new manufacturing avenues.
These sustainability considerations position PET preform injection molding as a key player in contemporary ecological initiatives, making it an essential topic for manufacturers and industry experts.
6. PET Preform Injection Molding Machines
A variety of machines are designed explicitly for PET preform injection molding, and understanding these options is vital for professionals in the industry.
Types of PET Preform Injection Molding Machines
PET preform molding machines can vary significantly in function and capacity. Common types include:
- Hydraulic Injection Molding Machines: These machines utilize hydraulic systems for generating the pressure needed to inject the molten PET into the mold.
- Electric Injection Molding Machines: These machines offer superior energy efficiency and precision, ideal for high-volume operations with repetitive identical products.
- Hybrid Injection Molding Machines: Combining both hydraulic and electric systems, hybrid machines are becoming increasingly popular as they offer the advantages of both worlds.
PET Preform Hot Runner OEM
Key OEMs in the PET preform injection molding sector include Husky Injection Molding Systems, Sipa, and Mold-Masters. Each of these brands provides a comprehensive range of preform molds and injection equipment suited for diverse production needs.
Polymer Cleaning Technology – Your Hot Runner Experts
PCT is one of the largest independent providers of hot runner parts, repairs, and maintenance for all brands of PET preform hot runners. Able to provide a wide array of PET parts and services for:
HUSKY™, MHT™, MOLDMASTERS™, HUIYUAN™, HUAYAN™, CHENG HSONG™, SACMI™, SIPA™
Custom hot runner parts and upgrades are always available, with the ability to reverse engineer any hot runner component, only a sample is needed to begin your project. Whether looking for replacement parts, system upgrades, or complete PET preform hot runner refurbishment, our range of PET Preform Hot Runner solutions has you covered. Give us a call today at (908) 281-0055 and experience the difference that precision-engineered hot runner components can make for your production line.
PET preform injection molding stands out as a highly efficient and versatile technology that offers numerous advantages for various applications. The process allows for the production of lightweight, durable, and visually appealing preforms that meet strict quality standards. The unique properties of PET, such as its recyclability, clarity, and strength, position it as a leader in sustainable packaging solutions.
By understanding the intricacies of the PET injection molding process, industry professionals can harness its capabilities to drive innovation and operational excellence in their respective fields. As sustainability becomes increasingly integrated into manufacturing practices, PET’s role in fostering a circular economy will be paramount, ensuring that its applications continue to thrive in alignment with future environmental goals.
*This information is to be used as a general guideline only. Speak to your system manufacturer directly for verified information regarding your Hot Runner System.
For more in-depth insights to PET Injection Molding, and PET Material, consult verified resources such as:
Geyer, R., Jambeck, J. R., & Law, K. L. (2017). Production, use, and fate of all plastics ever made. Science Advances, 3(7), e1700782. Link
Pacheco, A. M., & Ramos, J. V. (2018). Advances in the production of PET from renewable resources: New routes and technologies. Journal of Chemical Technology & Biotechnology, 93(1), 215–224. Link
Ehrenstein, G. W. (2001). “Polymeric Materials: Structure, Properties, Applications.” Hanser Publishers.

Find this information useful? Share with friends & colleagues:
Contact Information:
Polymer Cleaning Technology, Inc.
sales@polymercleaning.com
+1 (908) 281-0055