Valve Gate Systems vs. Open Gate Systems: Which Is Right for Your Application?
With hot runner plastic injection molding, the choice between valve gate systems and open gate systems is pivotal, influencing factors such as gate vestige, cycle time, part aesthetics, and overall production efficiency. Understanding the benefits and drawbacks of each system, along with their suitability for various applications, is essential for manufacturers aiming to optimize their molding processes.
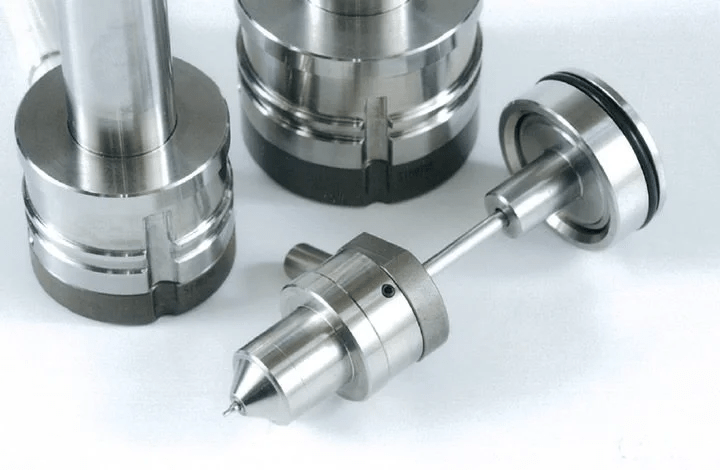
Contact +1 (908) 281-0055 or sales@polymercleaning.com to discuss your Hot Runner Systems today!
Benefits and Drawbacks: Gate Vestige, Cycle Time, Part Aesthetics
Gate Vestige:
Valve Gate Systems: These systems employ a mechanical valve or pin to control the flow of molten plastic into the mold cavity. The precise closure of the valve minimizes gate marks on the finished part, resulting in a smaller and less noticeable vestige. This feature is particularly advantageous for applications where surface appearance is critical.
Open Gate Systems: In contrast, open gate systems lack a mechanical shut-off mechanism, allowing molten plastic to flow freely into the mold cavity. This can lead to more prominent gate marks, as the plastic may leave larger vestiges upon solidification, potentially necessitating additional post-processing to achieve the desired surface finish.
Cycle Time:
Valve Gate Systems: The inclusion of a mechanical valve introduces additional steps in the molding cycle, such as the opening and closing of the valve. These steps can slightly increase cycle times. However, the enhanced control over material flow often results in higher quality parts, which can offset the longer cycle times by reducing the need for rework or rejection.
Open Gate Systems: With a simpler design and no moving parts to control the flow, open gate systems generally achieve shorter cycle times. This makes them suitable for high-volume production where speed is a priority, and the aesthetic requirements are less stringent.
Part Aesthetics:
Valve Gate Systems: The precise control over the flow of molten plastic ensures uniform filling of the mold cavity, reducing the risk of defects such as sink marks, weld lines, and flow lines. This results in parts with superior surface quality, making valve gate systems ideal for applications where aesthetics are paramount.
Open Gate Systems: Due to the lack of flow control, open gate systems may experience variations in filling, leading to potential surface defects. While suitable for less complex parts, they may not meet the aesthetic standards required for high-precision applications.
Industries and Applications Benefiting from Each Technology
Valve Gate Systems:
Industries that demand high precision and superior surface finishes often prefer valve gate systems. Applications include:
- Automotive: Components such as interior panels and lenses, where appearance and dimensional accuracy are critical.
- Consumer Electronics: Parts like casings and housings that require intricate designs and flawless finishes.
- Medical Devices: Precision components that must adhere to strict aesthetic and dimensional standards.
Open Gate Systems:
Open gate systems are favored in applications where high production speed is essential, and aesthetic requirements are less stringent. Industries and applications include:
- Packaging: High-volume production of items like bottle caps and containers.
- Toys: Manufacturing of various toy components where minor surface imperfections are acceptable.
- Industrial Parts: Components where functionality supersedes the need for a flawless appearance.
Maintenance and Operational Considerations
Valve Gate Systems:
- Complexity: The mechanical components, such as valves and pins, add complexity to the mold design, necessitating regular maintenance to ensure optimal performance.
- Cost: The initial investment and maintenance costs are higher due to the sophisticated components and the need for precise control systems.
- Downtime: Maintenance activities can lead to increased downtime, affecting overall production efficiency.
Open Gate Systems:
- Simplicity: With no moving parts, open gate systems are simpler in design, leading to easier maintenance and lower associated costs.
- Reliability: The straightforward design reduces the likelihood of mechanical failures, contributing to higher reliability in production.
- Flexibility: Easier to set up and adjust, making them suitable for a variety of applications without extensive reconfiguration.
Valve Gate and Open Gate Systems: Real-World Examples
Based on the analysis of valve gate and open gate systems, the choice between the two depends largely on the specific requirements of the application, including aesthetics, cycle time, cost, and maintenance needs. Below are recommendations for when to use each system, along with real-world examples.
Valve Gate Systems: High Aesthetics & Precision Control
Recommended For:
- Applications requiring superior surface finish and minimal gate vestige
- Industries where precision and uniformity are critical
- High-value parts where reducing waste and rework is necessary
Example: Automotive Headlight Lens (Valeo or Hella Using Husky Valve Gate System)
Automotive manufacturers, such as Valeo and Hella, produce precision optical components like headlight lenses that must be crystal clear, free of marks, and highly uniform to ensure proper light diffusion. A valve gate system is used because it eliminates gate vestige, which could create distortions in the light path, affecting safety and aesthetics. Additionally, it reduces flow marks and weld lines, ensuring the part meets stringent optical clarity standards.
Open Gate Systems: High-Volume, Cost-Efficient Production
Recommended For:
- Mass production of simple, high-volume plastic parts
- Applications where minor gate marks are acceptable
- Faster cycle times and lower tooling costs
Example: Plastic Bottle Caps (Coca-Cola Using Mold-Masters Open Gate System)
A company like Coca-Cola requires the production of billions of plastic bottle caps annually. These caps do not require a flawless surface finish, as functionality is prioritized over aesthetics. An open gate system is ideal because it allows for faster cycle times, lower system complexity, and reduced maintenance costs. By using a Mold-Masters open gate system, manufacturers can optimize production speed while keeping costs down, ensuring that millions of caps are produced efficiently every day.
Decision-Making Factors
- If your application demands high surface quality, go with valve gate systems (e.g., automotive lenses, medical devices).
- If cost and speed are top priorities, open gate systems are the better choice (e.g., packaging components, bottle caps).
- Consider the long-term maintenance costs—while valve gates offer better part quality, they require more maintenance and higher upfront investment.
By understanding these factors, manufacturers can align their production strategy with the right hot runner system, ensuring both efficiency and quality in their final products.
Conclusion
Choosing between valve gate and open gate systems in hot runner injection molding hinges on specific application requirements, including desired part aesthetics, production volume, and budget constraints. Valve gate systems provide superior control and surface finish, making them ideal for high-precision applications, while open gate systems offer simplicity and speed, suitable for high-volume production where minor surface imperfections are acceptable. Collaborating with experienced hot runner manufacturers can further optimize the selection process, ensuring the chosen system aligns with production goals and quality standards.
*This information is to be used as a general guideline only. Speak to your system manufacturer directly for verified information regarding your Hot Runner System.
For more in-depth insights into valve gate and open gate hot runner systems, consult resources such as:
Manufacturer Websites, Documents, Blogs – Mold Masters, Husky, Maenner
Sandler, J., & Schledjewski, R. (2023). Polymers Journal.
Gim, J., Kim, B., Rhee, B., Choi, J., An, S., & Jung, K. (2018). ResearchGate.

Find this information useful? Share with friends & colleagues:
Contact Information:
Polymer Cleaning Technology, Inc.
sales@polymercleaning.com
+1 (908) 281-0055