Optimizing Hot Runner Temperature Control: Best Practices and Troubleshooting
Central to hot runner injection molding performance is precise temperature control, which ensures consistent melt flow, minimizes defects, and extends component lifespan. This article delves into best practices for optimizing hot runner temperature control, explores troubleshooting techniques, and highlights advancements in technology. Additionally, it underscores the significance of maintenance and introduces Polymer Cleaning Technology as a leading provider of hot runner parts and services.
The Importance of Precise Temperature Control in Hot Runner Systems
A hot runner system maintains plastic in a molten state within the mold using heated manifolds and nozzles. It eliminates the need for cold runners, thereby reducing scrap and increasing productivity. But its success depends heavily on keeping the melt at the optimal temperature throughout the process.
Key Benefits of Proper Temperature Control:
Consistent Part Quality: Prevents flow lines, sink marks, stringing, or incomplete fill.
Material Integrity: Avoids polymer degradation due to excessive heat or dwell time.
Cycle Time Reduction: Maintains flow characteristics that promote faster part filling and cooling.
Lower Scrap Rates: Reduces defects associated with thermal inconsistency.
Energy Efficiency: Prevents overcompensation and unnecessary heating.
Poor thermal regulation can offset the benefits of a hot runner system and result in increased downtime, wasted material, and high defect rates.
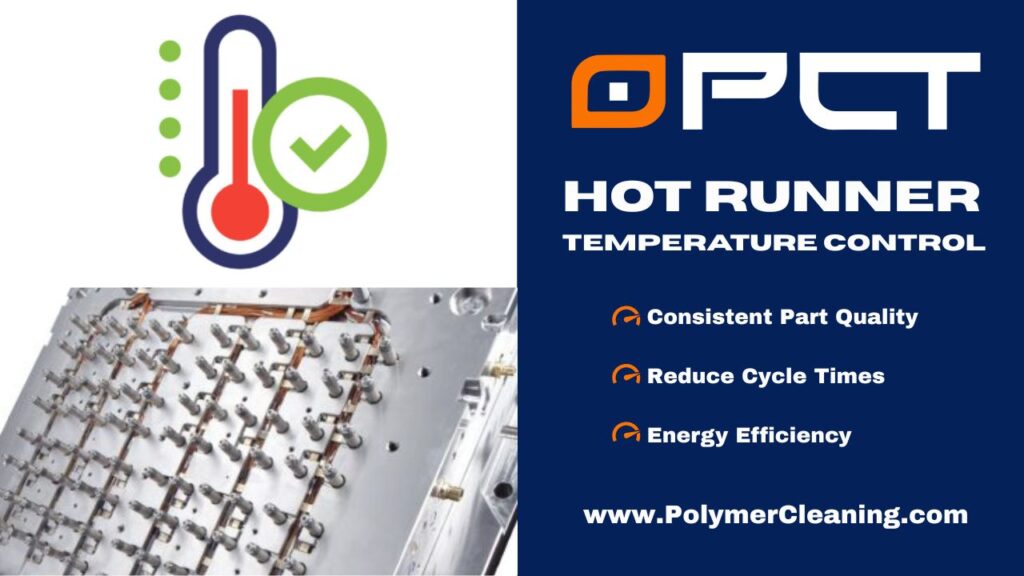
Contact +1 (908) 281-0055 or sales@polymercleaning.com to discuss your Hot Runner Systems today! Experts in Hot Runner System Repair and Maintenance for all OEM.
Best Practices for Optimizing Hot Runner Temperature Control
1. Upgrade to Smart Temperature Controllers
Modern controllers offer zone-specific control, auto-tuning, diagnostics, and alarm systems that maintain steady temperatures even during process changes. They can identify and compensate for real-time fluctuations and prevent system-wide issues before they escalate.
2. Ensure Accurate Sensor Placement
Thermocouples and RTDs should be installed near critical areas such as nozzle tips and gates. Proper sensor placement ensures accurate feedback and allows the system to respond to localized fluctuations.
3. Calibrate Regularly
Temperature sensors can drift over time. Regular calibration ensures they continue to provide accurate data. Calibration should be part of scheduled maintenance to verify temperature readings across all zones.
4. Use Zonal Heating Configurations
Dividing the hot runner into zones and using dedicated controllers allows you to manage temperature differences caused by complex geometries or material behavior.
5. Monitor System Data and Trends
Using software that tracks and logs temperature data across all zones enables predictive maintenance. It allows process engineers to identify minor inconsistencies before they affect production.
6. Select the Right Heater Types
Cartridge heaters, band heaters, and coil heaters each have specific applications. Selecting the correct heater design for manifolds and nozzles ensures efficient and uniform heat transfer.
Injection Molding Temperature Control Issues and Troubleshooting
Even the best-designed systems can encounter issues. Identifying the root cause quickly minimizes downtime.
1. Fluctuating Temperatures
- Possible Causes: Damaged sensors, power supply inconsistencies, or controller faults.
- Fix: Replace thermocouples, check wiring and connectors, update controller firmware.
2. Localized Hot or Cold Spots
- Possible Causes: Heater burnout, insulation degradation, or uneven heating element placement.
- Fix: Replace faulty heaters, re-insulate key areas, and ensure balanced zoning.
3. Material Degradation
- Possible Causes: Resin overheating or long residence times at elevated temperatures.
- Fix: Optimize setpoints, reduce dwell time, and purge systems regularly.
4. Sensor Failures
- Possible Causes: Electrical interference, wire breakage, or physical damage.
- Fix: Use shielded cabling, inspect wiring, and replace malfunctioning probes.
Advancements in Hot Runner Temperature Control Technology
Innovations in hot runner systems continue to focus on improving control, reliability, and integration.
1. AI-Driven Controllers
New systems utilize machine learning algorithms to predict and adjust setpoints based on material type, flow behavior, and ambient conditions.
2. Wireless and Remote Monitoring
IoT-enabled temperature controllers allow operators to track and adjust settings remotely. This reduces human error and speeds up troubleshooting.
3. Modular Heating Systems
Hot runner manufacturers now offer modular heater and sensor units, which simplify maintenance and reduce downtime during repairs or replacements.
4. Advanced Insulating Materials
Next-gen insulation reduces heat loss while protecting wiring and adjacent mold components, contributing to energy efficiency and better thermal consistency.
Preventive Maintenance with Thermal Optimization
Regular maintenance is essential for long-term performance and reduced operating costs.
Critical Maintenance Practices:
Scheduled Cleaning: Prevents carbon build-up and blockage.
Inspection and Replacement of Heaters/Sensors: Identifies degradation before failure.
Calibration of Control Systems: Ensures all temperature readings are accurate.
Electrical Testing: Verifies resistance and continuity in wiring harnesses and heating zones.
Preventive maintenance significantly lowers the risk of unscheduled downtime and defective runs.
When to Consider System Upgrades
Hot runner systems, especially older models, can become thermal liabilities over time.
Indicators You May Need an Upgrade:
Frequent heater or sensor failures, Uneven part filling or discoloration, Inability to maintain target temperature ranges, Increasing cycle times and scrap rates, Limited or outdated controller functionality
Upgrading to a newer temperature control platform or modular hot runner system often pays for itself in reduced waste and increased throughput.
Polymer Cleaning Technology: Leading the Way in Hot Runner Services and Parts
With a reputation for precision and reliability, PCT helps manufacturers keep their hot runner systems operating at peak performance.
Services Offered
Hot Runner Cleaning
Specialized chemical-free cleaning systems remove polymer residue without damaging metal surfaces.
Preventive Maintenance Programs
Tailored service schedules to suit production environments.
Component Repair & Refurbishment
Includes manifolds, heaters, nozzles, and temperature control systems.
Reverse Engineering & Custom Parts
Solutions for hard-to-find or discontinued OEM parts.
Parts Inventory
- Nozzle Tip Insulators
- Heaters (coils, bands, cartridges)
- Thermocouples
- Nozzle Tips
- Valve Pins
- Nozzle Housings
- Sealing kits
Hot runner temperature control is a foundational aspect of injection molding success. From ensuring material flow and preventing degradation to improving part quality and lowering costs, the value of precise thermal regulation cannot be overstated.
By leveraging modern technologies, performing routine maintenance, and upgrading systems when necessary, manufacturers can gain a competitive edge. Working with experienced partners like Polymer Cleaning Technology ensures access to high-quality parts, deep technical expertise, and service programs that safeguard productivity.
Whether you’re troubleshooting an aging system or setting up a new mold line, optimizing your hot runner temperature control strategy is an investment in long-term manufacturing excellence.
*This information is to be used as a general guideline only. Speak to your system manufacturer directly for verified information regarding your Hot Runner System.

Find this information useful? Share with friends & colleagues:
Contact Information:
Polymer Cleaning Technology, Inc.
sales@polymercleaning.com
+1 (908) 281-0055